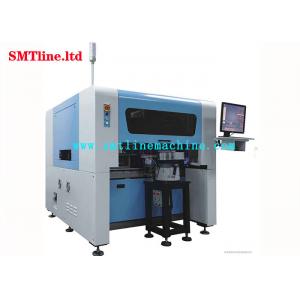
Add to Cart
Bulk LED Line Auto Insertion Machine AI used and new insert equipment 2 years warranty from cnsmt
Quick Detail
we supply all brand insert machine
Universal and panasonic brand avk3 rh2 ...
Theoretical velocity | 18000 / h (software system upgrade can be speeded up) |
Insertion loss rate | Less than 300PPM |
Insertion direction | The 0-360 degree increment is 1 degrees. |
Lead span | Double spaced 2.5mm/5.0mm/7.5mm or 3.5mm |
Substrate size | Minimum 50mm * 50mm, maximum 450mm x 450mm |
Substrate thickness | 0.79-2.36mm |
Component specification | The maximum height is 23mm, the maximum diameter is 10mm, and the maximum pin diameter is 0.8mm. |
Component species | Capacitors, transistors, triode, LED lights, button switches, resistance, connectors, coils, potentiometers, fuse seats, fuse wire and other vertical tape packaging materials. |
Length of shear foot of element lead | 1.5 + 0.3mm (short leg knife), 2 + 0.3mm (long sword). |
Angle of elbow of element lead | 10-35 degree (adjustable) |
Number of material stations | The 60 stop (the number of push to use stations) is optional (10-100 stations). |
Machine size (long * width * high) | Host size 1800mm x 1600mm x 2000mm |
Material station size | 500mm x 600mm x 760m |
Machine weight | 2000KG (40 station) |
Use power | 220V, AC (single phase) 50/60HZ, 2.0KVA/1.8KW (energy saving) |
System protection | Uninterrupted power supply (UPS) configuration can run for 15 minutes after power failure. |
Use power | 1.6KW (energy saving type) |
Use of air pressure | 0.6--0.8MPA |
Gas consumption | 0.3 cubic / minute |
Use of ambient temperature | 5-25 degrees |
Machine noise | 65 decibels |
Hole position correction method | Machine vision system, multi point MARK visual correction. |
driving system | AC servo, AC motor |
Data input mode | USB interface input (EXCEL document format) |
Control system | Chinese operation interface (WINDOWS system control platform) LCD monitor |
Component density | The 1mm distance between the components and the distance between the patch element and the hole can not be less than 3mm |
Worktable operation mode | Clockwise and counterclockwise direction |
Transmission mode of PCB | Manual / automatic optional |
Feature
Product Name: | smt Auto Insertion Machine |
Used for: | smt assembly full line |
Warranty: | 1 Year |
Shipment | by air |
Delivery Time: | 1-2Days |
Our Main Market | Whole of the world |
Packaging details:foam and carton
Delivery time:Within 1~3 working days
Shipment
1. We ship to world wide
2. Most orders ship within 1~7days after payment
3. Item shipped from china mainland using airmail by EMS, UPS, DHL, TNT or Hong Kong post, we accept the customer’s shipping request
4.100%T/T before shipment, after we shipped the goods, we will email you the shipping information
5.WE sell and buy used equipment long-term
Maintenance
Maintain the working stability and accuracy of the equipment, extend the life of the equipment, and maintain the high efficiency and high quality output of the equipment.
1, daily maintenance
Check whether the machine has loose, damaged or missing parts.
Check the indicator lights and keys are normal.
Check the filtration condition of the air filter cup and remove the water or sundries.
Check whether the pressure is 60-90PSI.
Clean, lubricate X, Y Guide (10# oil).
Check the tightening of the steering wheel of the rotating table.
Check the rectangle of the rotating table.
Clean and lubricate plug-in head tools and cylinder rods (with 5# oil).
Clean, check and lubricate the cutting point movement point (with 5# oil).
Clean the BEC lens with clean and soft cloth.
2. Zhou Baoyang
Check the filter net in the clean I/O box.
Check the height of the oil surface of the compressed air filter and the mist sprayer, and check the oil dropping rate of the mist sprayer (1 drops /3 minutes).
Clean and lubricate positioning system X, Y guide bar, lubricate clean guide bar sleeve (with 10# oil).
Clean and lubricate X, Y wire rod (with blue oil).
Clean, check, lubricate plug-in knives, drive rod connection points, shaft and other active parts (with 5# oil).
Check the wear of cutting shear knives, clean and lubricate the shear mechanism.
Check the correction ability of BEC.